FQAS |
|
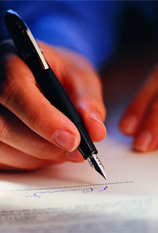 |
|
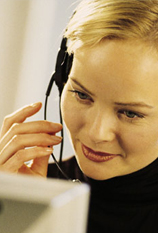 |
|
|
|
Current Location£ºFQAS |
 |
|
|
|
Brief Introduction |
|
|
|
How many molds do you make annually! |
Averagely, we make about 800 to 1,200 molds annually. |
|
How many shifts do you operate every day! |
For CNC, EDM and Polishing Departments, two shifts; Mold Shop depends on the emergency; the others are one shift. |
|
How long is the lead-time for a mold! |
It¡¯s hard to say. It will depend on the mould¡¯s size, complexity and design. Usually, the lead-time is about 4 to 8 weeks. |
|
Facilities & Technology |
|
|
|
How do you maintain your advanced machines! |
We appoint the experienced and skilled staffs to maintain these machines. |
|
Have the operators been trained specially! |
Yes, they have. |
|
Where do you buy mold base! |
Usually we buy them from Long-Kee Company or Ming-Lee Company. |
|
How do you do the texture/text/heat-treatment /nitriding and so on! |
We usually arrange the cooperative subsidiary factories to do that. |
|
How do you monitor the process! |
Our Project Dept. appoints project manager and engineer to handle every project progress and to communicate with customers. |
|
Which standards do you use, Metric or English! |
Both of them are OK. We can use the standards requested by customer. |
|
What do you think is the most important in mold making! |
We think quality and attitude is the most important. We service all customers in high quality and honest attitude. |
|
Can you provide the steel certificate and heat-treatment certificate! |
Yes, we can. The steel supplier and heat-treatment factory can provide the certificates. |
|
Do you use graphite or copper to be electrodes! |
We use both of them. |
|
Human Resource & Working Environment |
|
|
|
Where did you employ your staff! |
We seek qualified, experienced and high-educated employees from talent marketing or college. |
|
Have your employees been trained! |
Yes, they have. We provide internal training for every new comer from the beginning. |
|
How many percent of the talent flow in your company each year! |
The percentage is quite small, only about 2-3%. We think the stability of workforce can maintain a good productivity. |
|
Terms of Shipment & Payment |
|
|
|
Can you explain your terms of payment! |
For new mold, 40% deposit, 30% on first short, 30% before delivery. For modify mold, 100% one week upon the approval of the updated samples. For prototype mold, paid 50% when place P.O, and the balance before samples or mold delivery. |
|
How do you pack the mold! |
It all depends where the moulds are shipped. For the mould inland: general packing method. For the mold exported oversea: we pack it strictly according to the standard of export regulation. |
|
After-Sale Service |
|
|
|
If there has problem on the mold after the shipment, what did you do! |
This kind of matter has never happened to us before. But if it happens and it is our fault, we pay all the cost without any bargain. |
|
Who pay the cost of modification! |
The small changes are free. But for the great changes, if it is our fault, we pay; customer¡¯s fault, they pay; both fault, both pay. |
|
Do you make spare part for customer! |
Yes, we do. If customer request. |
|
|
|
|
If you have any questions about Honesty Mold, please do not hesitate to e-mail us. |
| |
|
|